Drilling has been a very slow operation historically since the days of HSS drills. Modern metal cutting industry made a tectonic shift from HSS to Solid Carbide at the start of this century.
The metal cutting industry in India adopted this change around the same time since it was modernising with machining centres. It was around this time that it was realised in the industry that SC drills need a totally different approach for their construction and holding, since SCDs are stiffer and harder than HSS drills and thus bend much less. At similar feeds, a cutting speed of about 100 m/min, is possible with SCDs compared to max. 15 m/min. with HSS drills.
The tool life with SCDs is normally 20 times longer than with HSS drills. The cost per hole and the total cost are in general 60 – 80% less as compared to HSS drills. Figures well worth considering.
For the SC drills to achieve all this with process security and no breakage at the above elevated parameters. It was found necessary to change the geometry of the drill point in a
drastically.
In a modern SC Drill the Chisel edge is practically eliminated and the main cutting edge almost reaches the center point, which enables the drill to give longer drill life and higher productivity due to lower thrust and Torque; Better tolerances are achieved on the hole (H8-H10), due to the Drill being manufactured on modern 5 to 6 axes CNC Tool & Cutter Grinders in one set up.
For achieving this precision Aayudh makes SC drills to m7 tolerance. Further Aayudh can customize drills to give H8-H9 tolerances.
Another factor which is very important for drill performance and security is the Tool holding used for the SC drill at modern parameters of Vc = 80-120 m/min &fn/rev = 0.15-0.3; here the TIR of the drill is vital to avoid drill breakage maintain the hole tolerance(H8-H9) and get good surface finish(3.2 Ra). For this high precision Hydraulic holders which maintain TIR less than 4-5microns contribute in maintaining process security, compared with ER collet holders.
Aayudh has further optimised the total drill geometry based on applications in different materials; – ISO P(steels), K(cast iron &SGIron),M(SS),N(aluminium),S(heat resistant super alloys,titanium,etc) ;
By optimising we mean Drill point Geometry, Drill Flute geometry,and Drill coatings.
Drill coatings play an important role in reducing cutting forces built-up edge and protect the edge at elevated temperatures. Consequently different coatings are used for different materials, so when Aayudh optimizes a drill, it optimizes all three aspects.
For eg: We show our approach to designing and manufacturing an optimized drill for steel machining- Aayudh P.
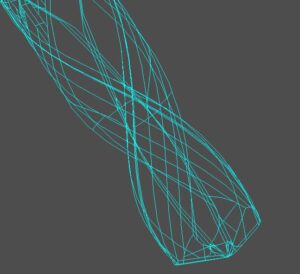
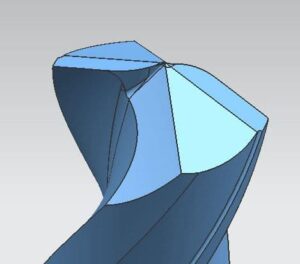
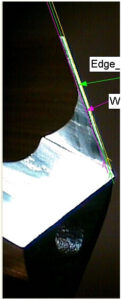
Similarly Aayudh have optimized drills for SS – Aayudh M
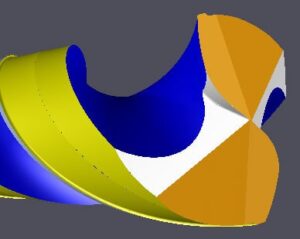
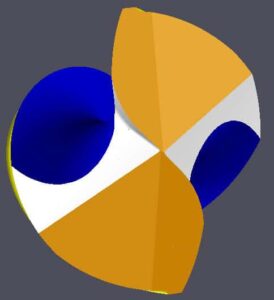
For heat resistant super alloys – ISO S for which Aayudh have the optimized drill Aayudh S, which is very similar to Aayudh M expect for the difference in edge treatment to reduce the cutting forces and withstand higher temperatures when drilling in work hardening materials.
For Drilling in ISO N materials- For aluminium drilling Aayudh has optimized the drill geometry to cater for partial core hole applications in pressure die casting components common in two ,three, four wheeler industry. Our approach to Aayudh N is shown below.
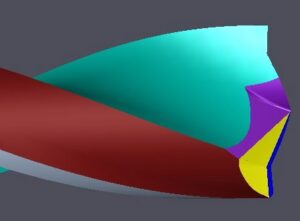
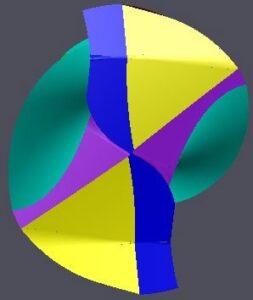